We transform matter by applying circular economy principles
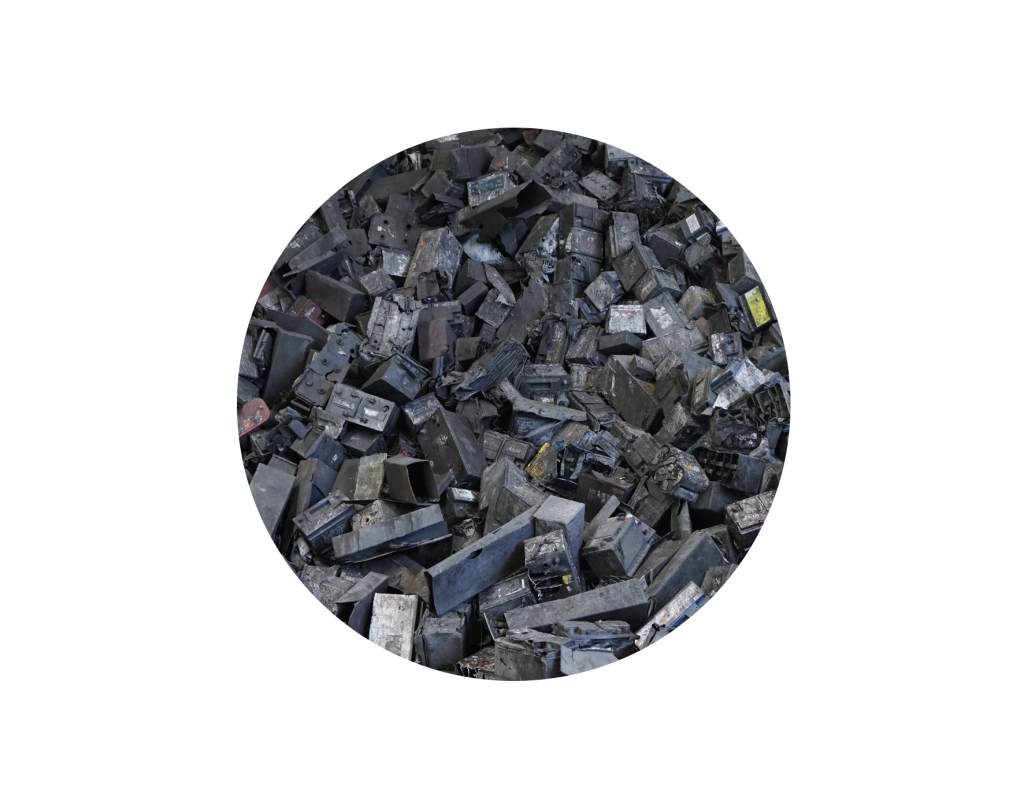
1^ Reduction phase , separation and desolphoration
We recover, receive and accurately inspect any kind of lead material, the next step is the reduction phase in which we divide constitutive components of scrap lead batteries.
Thanks to a complex and modern technology, we obtain lead carbonate in order to greatly reduce the presence of sulphur. In combination with the connected crystallization plant, we reduce the amount of sterile waste sent to authorized refuse centers by over 50% and we guarantee full compliance with SOx chimney emission requirements.
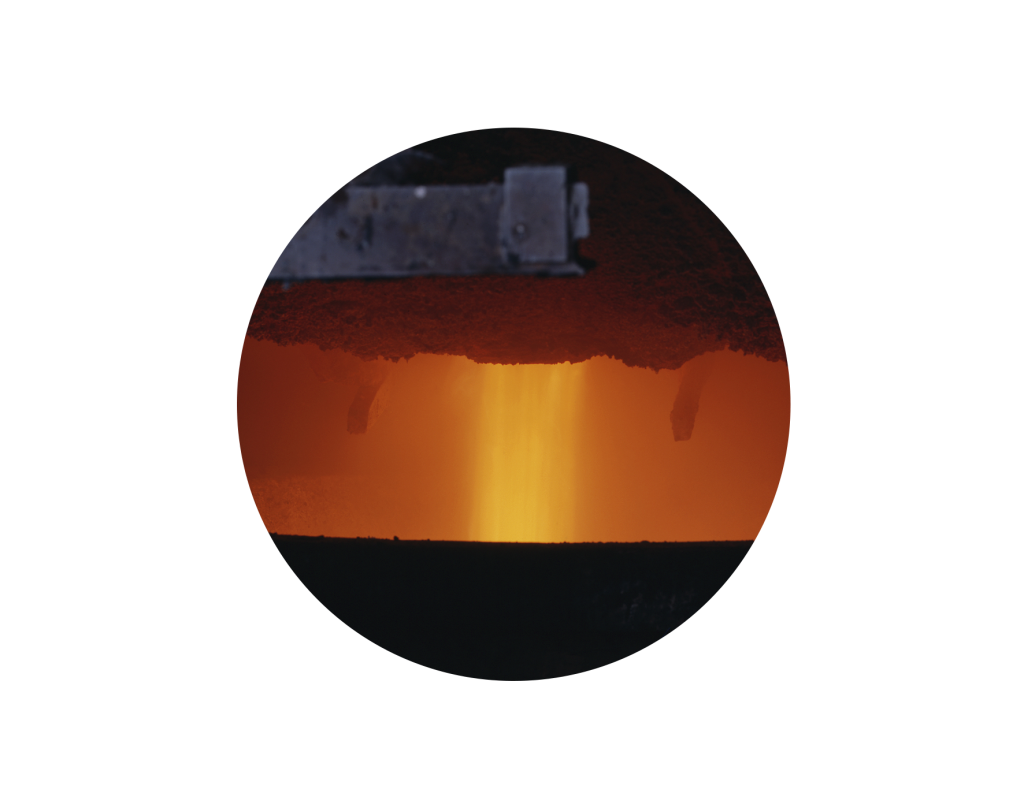
2^ Smelting
The pretreated materials with a high lead level are transferred to rotary melting furnaces which reach the melting point at high temperatures, by using a mixture of oxygen and methane according to a precise stoichiometric ratio. The material loaded into the furnaces is then transformed into melted raw metal.
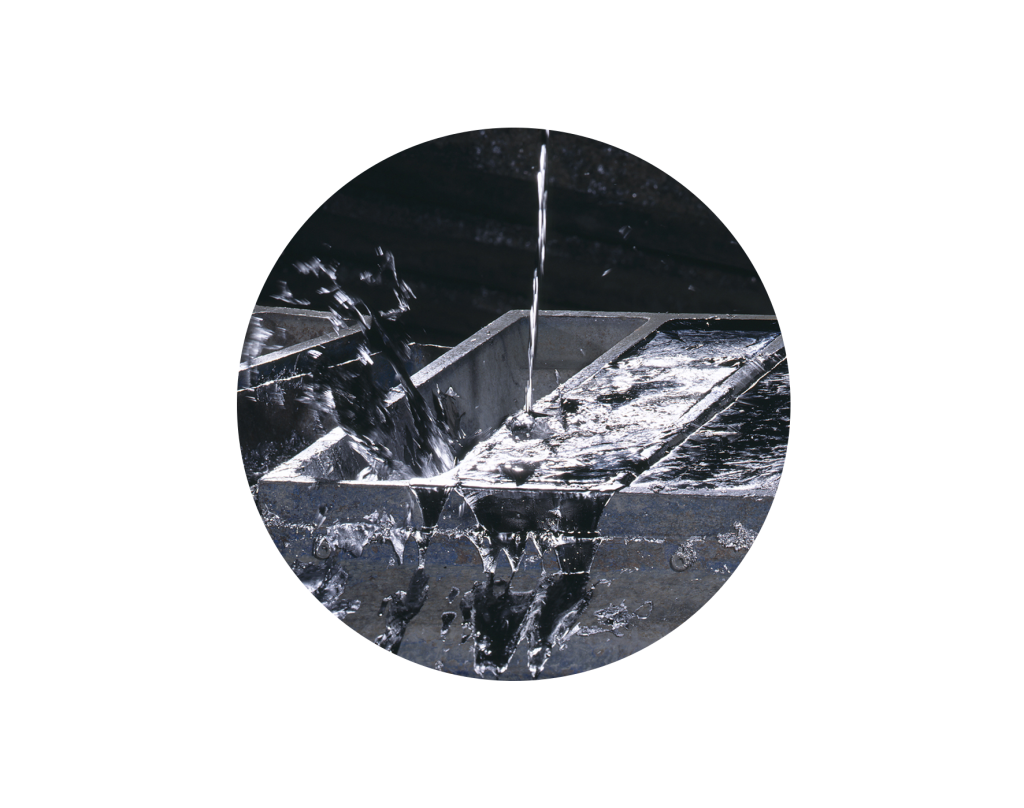
3^ Refinery and casting
In the refinery department, we refine rough melted metal and we analyse it by a spectrophotometer. In this phase, the semi-finished product can be integrated with further elements that enrich its properties, according to customer specifications and their final uses. Once we verified the correspondence of the parameters obtained to the required alloy, we proceed with the casting of the lead in the form of ingots and bullions.
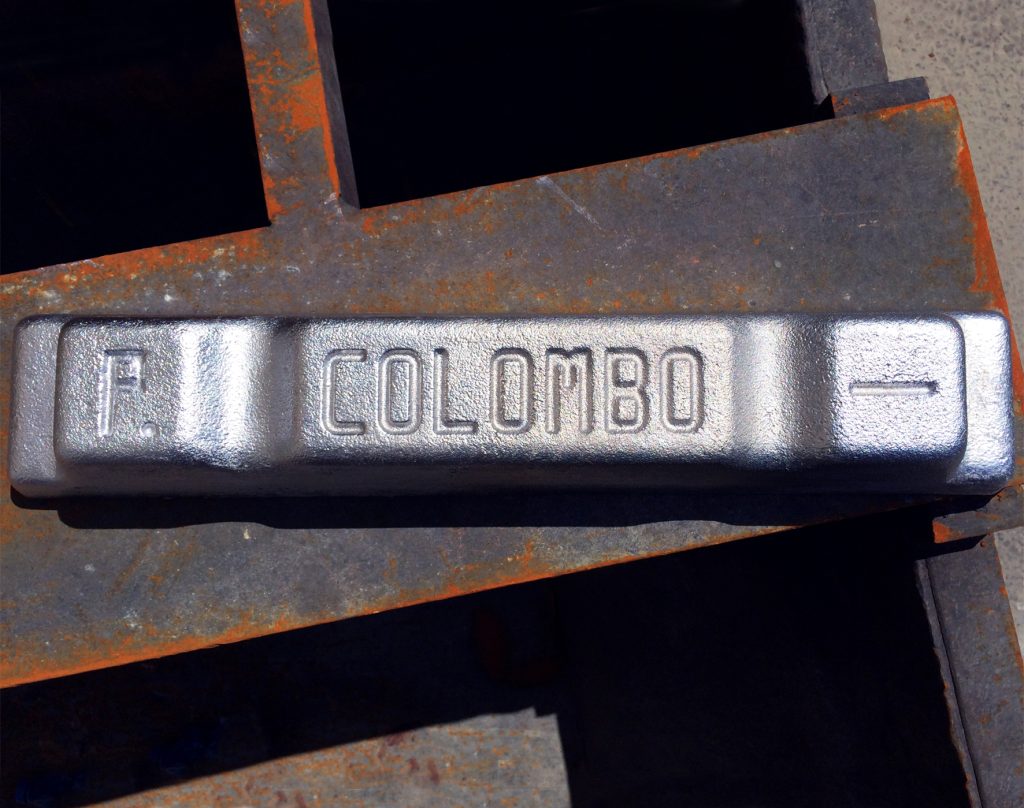